10 Principles to Reduce Casting Defects
In the production process, foundry enterprises inevitably encounter casting defects such as shrinkage, bubbles, segregation, etc. This will result in low casting yield, and re-reflow production faces a lot of manpower and power consumption. How to reduce casting defects is a problem that has always been concerned by casting professionals.
For the problem of reducing casting defects, John Campbell, a professor from the University of Birmingham in the United Kingdom, have experienced many battles and has unique insights on reducing casting defects. As early as 2001, Li Dianzhong, a researcher at the Institute of Metal Research of the Chinese Academy of Sciences, carried out the organization simulation and process design of the thermal processing process, which was completed under the guidance of Professor John Campbell.
Hope the list of ten guidelines for reducing casting defects by international foundry master John Campbell is helpful to colleagues in the foundry industry.
1. Good castings start from high-quality smelting
We must prepare, inspect and process the smelting process before pouring the castings. If required, the lowest acceptable standard can be used. However, a better option is to prepare and adopt a smelting plan that is close to zero defects.
2. Avoid turbulent inclusions on the free liquid surface
This requires avoiding excessively high flow velocity at the front free surface (meniscus). For most metals, the maximum flow rate should be 0.5m/s. Meanwhile, for closed gating systems or thin-walled parts, the maximum flow rate will be increased appropriately. This requirement also means that the drop height of the molten metal cannot exceed the critical value of the “static drop” height.
3. Avoid laminar inclusions of surface condensate in molten metal
This requires that during the entire filling process, there should be no front end of any metal flow to stop the flow in advance. The liquid metal meniscus in the early stage of filling must be kept in a movable state, and not affected by the thickening of the surface condensate, which will become part of the casting. Thereupon, to achieve this effect, the front end of the molten metal can be designed to continuously expand. In practice, only the “uphill” ante bet can achieve a continuous ascent process. (For example, in gravity casting, flow upwards from the bottom of the sprue). This means: bottom injection gating system; no “downhill” form of molten metal falling or slipping, no large-area horizontal flow and no front-end flow stop of molten metal due to dumping or waterfall flow.
4. Avoid air pockets
Avoid air bubbles generated by the pouring system from entering the cavity. It can be achieved by the following methods: reasonable design of stepped sprue cups; reasonable design of straight runners to fill up quickly; reasonable use of “dams”; avoid using “well” or other open gating systems; use small cross-section runners or the sprue uses ceramic filters near the junction of the runner; uses a degassing device; do not interrupt the pouring process.
5. Avoid sand core pores
Avoid the bubbles generated by the sand core or sand mold from entering the molten metal in the cavity. The sand core must ensure a very low air content, or use proper exhaust to prevent the sand core pores. Unless you can ensure complete drying, you can not use clay-based sand core or mold repair glue.
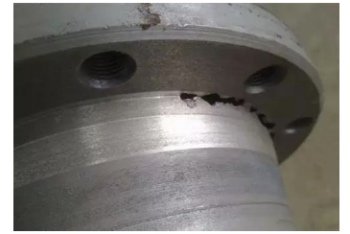
6. Avoid shrinkage
Due to the influence of convection and the unstable pressure gradient, castings with thick and large cross-sections cannot achieve upward feeding. Therefore, it is necessary to follow all the feeding rules to ensure a good feeding design. At the same time, use computer simulation technology for verification, and actually cast samples. Control the flash level at the junction of the sand mold and the sand core, the thickness of the mold coating (if any), and the alloy and mold temperature.
7. Avoid convection
Convection hazards are related to the setting time. Both thin-walled and thick-walled castings are not affected by convection hazards. For medium-thickness castings: reduce convection hazards through casting structure or technology; avoid upward feeding; turn over after pouring.
8. Reduce deflection
Prevent segregation and control it within the standard range, or the area allowed by the customer to exceed the limit. If possible, try to avoid channel segregation.
9. Reduce residual stress
Do not quench the light alloy with water (cold water or hot water) after solution treatment. If the casting stress does not seem large, polymer quenching media or forced air quenching can be used.
10. Given reference point
We must give all castings a positioning datum point for dimensional inspection and processing.
Yide casting is a leading casting foundry in China, with 27 years’ experience, produces top quantity ductile iron castings. If you are interested in our casting fitting, please send us a drawing file, and feel free to get a quite quote.